Micropress
Micropress maximizes operations with the Midmarket Print Suite
Learn how through continuous feedback on job costs and job types, Micropress can estimate with more speed and accuracy.
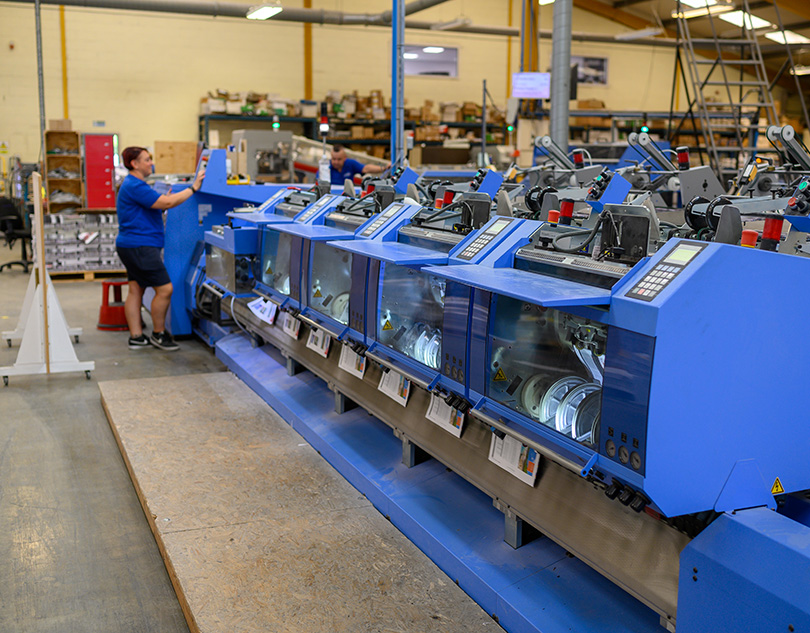
“We are seeing greater productivity and planning greater efficiencies throughout our operation.”
Rob Cross,
Commercial Director, Micropress
About the company
Micropress Printers Ltd is one of the largest independent commercial printers in the UK, specializing in products such as leaflets, brochures, catalogs, case-bound books, magazines, mailers, and more. The company has retained independent ownership and consistently expanded its services in response to the needs of its customers. With over 40 years of knowledge and experience in the print industry – ranging from litho through to the development of digital print – Micropress has adapted itself to an increasingly tough print marketplace.
In recent times, the company has developed a personalized account management service, providing its customers with an individualized business relationship and the delivery capabilities of one of the largest sheet-fed litho commercial printers in the UK. It has customers across the U.K., which it serves from its two print production units – located in Southwold and Lowestoft in Suffolk, East of England. With its 24-hour production operations, these facilities can service an extensive number of clients with a wide range of products, all within short turnarounds. Micropress serves customers that vary from small companies to print management companies and print buyers.
The company has invested in the systems necessary to swiftly process different types of orders, including online sales direct from customers through a dedicated portal. In addition, the company has a substantial paper warehouse. By consistently buying in bulk, it can easily cope with a fast turnaround on almost any job and pass the cost savings over to its customers. Micropress usually holds up to £500,000 worth of paper at any one time.
The company’s printing operation includes three Heidelberg B1 presses, one Heidelberg B2 press, and a Xerox® iGen® digital production system that is driven by an eProductivity Software Fiery® digital front end (DFE). Micropress Printers Ltd. is one of the UK’s largest independent print suppliers, with an annual turnover of £17 million and 170 employees.
The company produces a wide variety of commercial print spanning from short-run leaflets to large-run high pagination catalogs and everything in between. The company services many different sectors and markets, working with a broad range of end users and customers, including, publishers, print management companies/brokers. The company also serves as a trade printer fulfilling other printing companies’ overflow or specialized printing needs. Quick turnaround, along with high quality, is a key to the value of Micropress’s service offering, with print turnarounds averaging from 3-5 days – although that varies from a week for large projects down to same-day turnaround on short-run digital print.
The challenge
Staying ahead of growing business volumes and challenges on production efficiencies by updating MIS capabilities.
Key requirements
The best fit for our business
“We looked at what was available on the market and decided eProductivity Software was the best fit for our business,” Cross says, and he found the Suite’s estimating, financial management and PrintFlow® dynamic scheduling features proving to be superior to other systems Micropress considered.
Micropress was especially impressed by the Midmarket Print Suite’s tracing of jobs in progress and the flexibility of the scheduling system that allows optimization of a production workflow and throughput maximization. The Suite’s automatic and accurate collection of up-to-the-minute production data includes counts, press status, speed, and other critical information directly from the equipment. It is machine- and brand-independent, and the way it works is tuned to the printing press it is hooked up to. “The dynamic scheduling component, for example, gives you the impression it’s clever. If you didn’t know any better, you’d be excused to believe it actually ‘thinks’
through certain decisions – it’s all non-linear and fed by the data each machine generates,” Cross explains.
As PrintFlow® dynamic scheduling is a rules-based system, the software is able to continuously interpret recorded data in real-time and translate that into strategic business actions. Cross explains how his Suite could, for example, prefer to run a job that is supposed to go to bindery tomorrow at 5:00 p.m. before a similar job that is
supposed to go to bindery tomorrow at noon, based on the fact that the job due at 5:00 is printed on media that requires a longer drying time. “It finds the ways to have the production environment as a whole run at its optimum – globally, not only on a machine by machine basis,” Cross said.
This doesn’t just benefit production efficiency but has important effects on estimating costs of a job, invoicing, equipment usage, media and ink consumption.
Better, quicker decisions
Micropress has been using the Midmarket Print Suite for six months now, and although the system hasn’t been rolled out across all of the company’s processes, it’s already seeing some spectacular benefits. “We’ve become much better at estimating,” says Cross. “Estimating is crucial to the business. Getting that right is the biggest thing. Because of the Suite’s continuous feedback about the actual costs of a job or type of job, we can check that we are estimating accurately.”
It has also enabled Micropress to easily recognize – through increased visibility – which specific areas are potentially more profitable than others. ePS Pace, the core of the Midmarket Print Suite, streamlines key administrative work such as accounts payables tasks. “Another big improvement we’ve seen in the past few months is the reduction of processes involved in invoicing,” explains Cross.
“It used to take three people to process our invoices with our previously installed system, now it only takes one person.” Getting to that level of automation and labour savings in invoicing does require that the information which is fed into the system needs to be clean at the input side. For this reason, Cross does not deny that adopting a new MIS or ERP system takes time and is best done in phases.
Micropress so far has been focusing its Suite implementation on the most important part of its business, but there are additional opportunities to streamline operations to come, such as bringing Suite tools for inventory management online, along with fully integrating the company’s Fiery Driven™ digital printing operations with the Suite so its digital production information automatically flows through the Suite.
With those future capabilities of the Suite still to come to fruition, “We expect big benefits to lay ahead,” according to Cross.
“Getting estimating right is the biggest thing. Because of the Suite’s continuous feedback about the actual costs of a job or type of job, we can check that we are estimating accurately.”
Rob Cross,
Commercial Director, Micropress Printers LTD